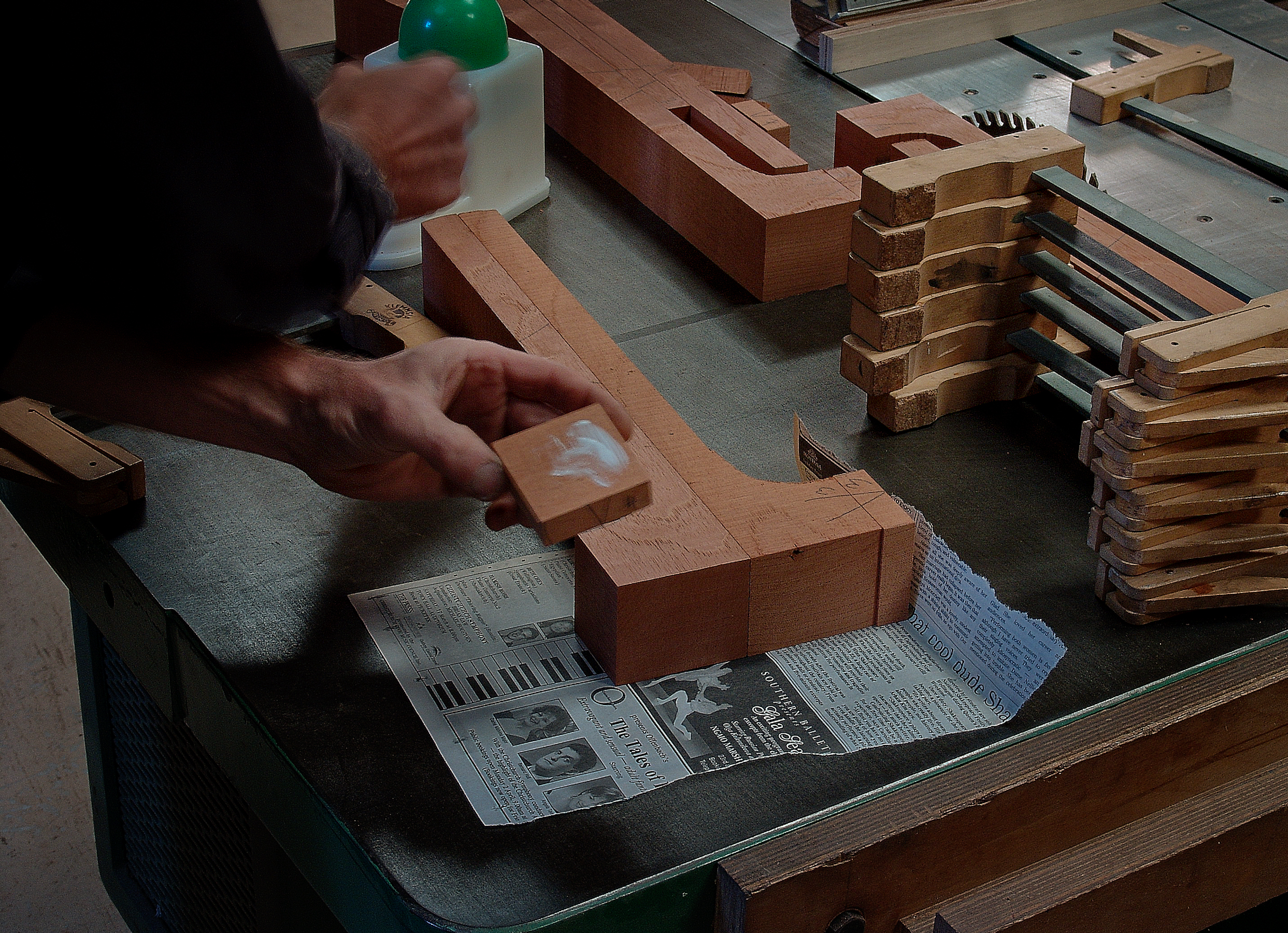
In the process of building the heals for a series of Mahogany necks.
When a musician strikes the strings of an instrument the effect of the vibration is determined by the neck, The neck facilitates the energy allowing it to pass through the whole body of the instrument, ultimately the neck calls the shots. If the timber used to make the neck is not efficient and has no musical characteristics then the performance of the instrument will suffer. Tonewood does not just relate to the soundboard, the whole instrument relies on the various materials used and how they relate. This is true to both acoustic and electric instruments.
The setting up of a neck decides the feel of the instrument. When I discuss the build of an instrument with the musician often they have very specific requests as to the neck setup. As an example : I built a couple of electric guitars for a classically trained musician, he required a much wider neck and didn't want any decals on the fret board except for the 12th fret, also the gauge and action of the strings were heavier than what most guitarists would request.
For a custom made guitar musicians can choose the finger board radius, neck profile (the shape of the back of the neck), neck size and width, fret type, timbers for fingerboards and scale length.
Note : Cleaning fretboards, in most cases I use kerosene, good practice is always test a small area before proceeding. Do not use silicon spray anywhere on your guitar and that includes, Mr Sheen or any similar products.
The reason for not using silicon spray is if your instrument needs any refinishing work the silicon spray interferes with the finish, resulting in fish eyes where the lacquer won't adhere to the surface.
My preferred truss rod system is a drooped steel rod in a channel formed in the neck with a well fitted wooden cover strip, this traditional method requires more work, but is free from vibration and lighter in weight. In the past and sometimes I use a threaded rod in an aluminum channel, this is suitable for some instruments, these tend to be a little heaver in weight.
My view gathered from years of observing failed twin rod systems is, that the double acting twin rods typically fail because they are installed incorrectly. In 25 years of guitar repair work on thousands of instruments I have seen only two guitars that would have benefited from a twin truss rod system. You almost never see a guitar where the neck is bent backwards. The double acting truss rod may appear to be a benefit, in fact it is a redundant technology.
Supplier no: | Crown Width | Crown High |
---|---|---|
Dunlop 6000 | 0.118 | 0.058 |
Dunlop 6100 | 0.110 | 0.055 Jumbo |
Dunlop 6105 | 0.090 | 0.055 |
Dunlop 6110 | 0.115 | 0.050 |
Dunlop 6120 | 0.114 | 0.051 |
Dunlop 6130 | 0.106 | 0.036 |
Dunlop 6140 | 0.106 | 0.039 |
Dunlop 6170 | 0.099 | 0.043 Medium |
Dunlop 6330 | 0.063 | 0.028 Small |
Jescar 45100 | 0.100 | 0.045 |
Jescar 47095 | 0.095 | 0.047 |
Jescar 47104 | 0.104 | 0.047 |
Jescar 50078 | 0.078 | 0.050 |
Jescar 51108 | 0.108 | 0.051 |
Jescar 55085 | 0.085 | 0.055 |
Jescar 55090 | 0.090 | 0.055 |
Jescar 57110 | 0.110 | 0.057 |
Stew-Mac 146 | 0.106 | 0.036 |
Stew-Mac 149 | 0.103 | 0.046 |
Stew-Mac 150 | 0.110 | 0.053 |
Stew-Mac 154 | 0.100 | 0.050 |
What I am doing here is finishing the fret ends to make for more comfortable playing, this also prevents strings from catching.
Birds mouth neck join. After I machine cut the joints, a little fine tuning with a sharp chisel to get the correct head angle and a tight fit.
Birds mouth neck joins with their headstocks ready for shaping.
The first stages of building a UEB neck, with plans, stocks and template.
Using a spoke shave to shape the neck of a six string electric bass.
Ebony is one of the nicest timbers to play on, as it has natural oils preventing strings from glitching. It is one of the harder timbers and thus doesn't wear so easily.
Slotting the fingerboard by hand for a 9 string fan fretted bass.
With my 9 string bass guitars, to increase the neck stiffness I use twin truss rods and three graphite bars. The template to the right is for the machine heads and the final headstock shape.
Return to the top of the page